COFASTRANS is born from many years of industry experience and backed by research, with the aim to resolve the challenges and inefficiencies faced by port operators and shipping companies globally.
There has been no positively revolutionary development to ship-to-shore container handling since the start of containerisation in the 1960’s.
New and significantly larger container vessels are continuing to be introduced by shippers on the world’s main shipping routes, in attempts to increase efficiency and bring down costs.
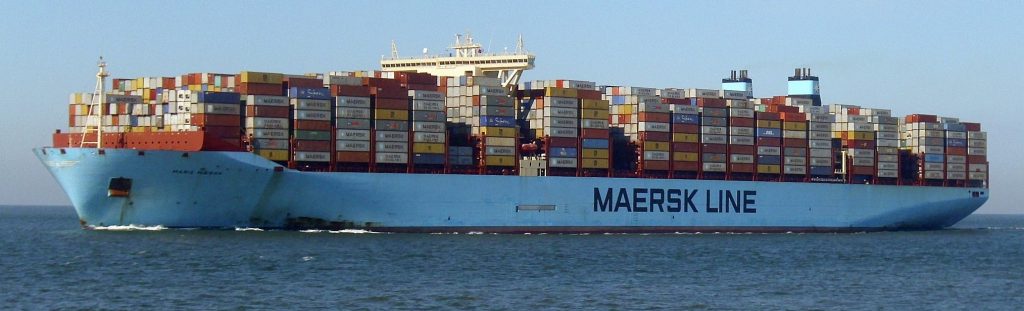
Old solutions for modern challenges
Larger vessels need longer berths and bigger ship-to-shore cranes. The industry standard procedure for port expansion is to extend berth lengths with straight line additions – some over 5kms long – and ever larger cantilever cranes, which inevitably take longer to load and unload the larger vessels.
This approach has introduced inefficiencies for port operators and shippers alike.

Map Data Google, DigitalGlobe
To meet their profit targets, the shipping lines need reduced time in port and faster cargo handling. The crane trolleys must move faster to unload containers at the same rate from the wider ship, yet speeds of movement within modern cranes are already at levels that make it difficult to achieve any increase.
Extremely long lines of ship berths are inefficient in terms of traffic management and can be environmentally damaging.
The layout is not designed for the high volumes of containers that are unloaded from each vessel, causing congestion and handling delays in the stack management system.
Meanwhile, some ports are left behind as environmental sensitivity or constraining urban developments restrict the port from further expansion using typical design solutions.